The Effect of Temperature on the Life of Power Electronic Devices
Electronic components including solid state devices, resistors, capacitors, inductors and others are all susceptible to failure from overheating. The expected life of any component, and of any final product built from those components, is affected by the temperature at which they operate. In fact, a temperature increase of 10 degrees Centigrade is generally accepted as cutting the life of a device in half. Likewise, reducing the temperature by 10 degrees can double its expected life.
Why Temperature Matters
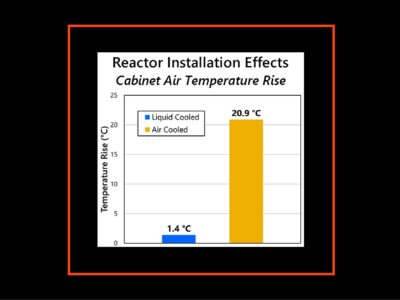
The field of reliability engineering provides many tools to estimate the mean time to failure (MTTF) and the mean time between failure (MTBF) for a product, and temperature is always a key factor in the calculation. That's why engineers specify a maximum operating temperature for electronic products.
For example, imagine a power management product designed to run in environments up to 50º Centigrade with an MTBF of, say, 20,000 hours. Operating at 60º will effectively cut its life in half. Alternately, if the environment were cooled to 40º, the MTBF could be extended to 40,000.
The temperature of an electrical component is affected by the ambient temperature of the environment, the heat produced by the component, and the efficiency of heat removal provided by the thermal system. Component temperature (and life) can be decreased by improving any of these factors. A more efficient component will give off less heat; an advanced thermal system is capable of quickly removing heat.
Consider a brief example: a group of people is attempting to move from one large room to another through a door. In this metaphor, each person represents a unit of heat, the door represents the cooling system, and the relative intensity of crowding or bottlenecking at the door represents the temperature. By decreasing the number of people (decreasing heat given off by the component), the crowding at the door (temperature) will decrease. Similarly, if door size or number of doors is increased (improving the thermal system), crowding at the door will also drop.
Methods for Temperature Control
Clearly, managing heat is a critical factor in the design of power electronics. Free convection cooling, the simplest means of heat removal, allows heat to dissipate directly to the stationary ambient air. Forced air cooling and liquid cooling are two methods used to improve heat dissipation compared to convection cooling. Forced air cooling uses fans to blow air across the surface of an electronic component, increasing heat transfer from the product to the surrounding air. However, due to low density and specific heat capacity, air is a relatively poor heat transfer medium. Increasing the number of fans or their speed increases the rate of transfer, but using a more efficient medium, a liquid, is more effective by a factor of 30 times or greater.
In a typical power conversion system, the amount of heat given off by the filter is second only to the switching device. Since electronic components are most often housed in a shared enclosure, in free convection and forced air cooling systems, heat given off by the switching devices and filter increases the cabinet ambient temperature, effectively decreasing the life of all the components housed in the common cabinet. One of the large advantages of liquid cooling (other than cooler operating temperatures) is that heat produced by the largest, hottest components can be removed directly through the coolant, minimizing the effect on cabinet air temperature. Read more about the benefits of liquid cooling here (see page 6 of the PDF for effects of air and liquid cooling on cabinet temperature).
Liquid Cooled Line Reactors
CTM Magnetics pioneered the design and development of liquid cooled line reactors nearly ten years ago and has now reached a point where those products are less costly than air cooled reactors. They're half the size and half the weight of competing air cooled line reactors, and they operate at nearly inaudible sound levels.
With more than 200,000 CTM products in service around the world—many running reliably in extreme environments—CTM can meet all your power quality needs. Contact us here